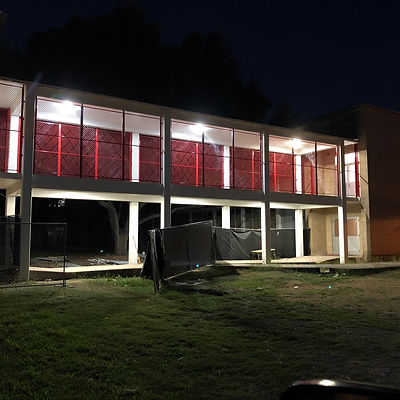
DAVIS MIDDLE SCHOOL
Serving over 47,000 K – 12th grade students in one of San Antonio’s most populous areas is no small feat for any school district. Originally founded in San Antonio’s W.W. White School District in the early 1880’s, Stonewall Jackson Middle School has shared a long and proud history of serving the community. In 1992, the San Antonio Independent School District renamed its Portwood campus near Fort Sam Houston in honor of Mr. Stonewall Jackson Davis. Mr. Davis was born in 1908 and received his Bachelor of Science degree in 1930 from Bishop College and his Master of Business Administration degree in 1946 from University of Texas in Austin. Since 1947, Mr. Davis has served as a longstanding leader of San Antonio’s African American community through his involvement with St. Phillip’s College faculty, Bexar County Chapter of the American Red Cross Board of Directors and as the first Black trustee on the San Antonio Library Board. Additionally, Mr. Davis was also a prominent member of the National Association for the Advancement of Colored People (NAACP), Alamo City Chamber of Commerce, Hemisfair Host Committee, United Way and the Texas State Teacher’s Association. As the population of students served by SAISD continues to grow, its administration has begun the process of upgrading and renovating its campuses utilizing its 2016 Bond Program funding. Included in the 2016 Bond Program, the District identified the need to upgrade and replace the main electrical distribution system in the original Davis Middle School building.
SAISD selected Joeris General Contractors to serve as the Construction Manager to construct the project. As part of a competitive subcontractor bidding process, Central Electric was selected to perform its electrical construction services including all major electrical systems, fire alarm, lighting controls and electrical gear distribution upgrades. Central Electric began its services and performed over 25,000 hours of work for the project. As described above, a critical component of this project was to upgrade and replace the main electrical distribution system in the original building. All aspects of the work required extensive planning and coordination with the owner given the school’s busy schedule. The Central Electric team developed creative processes for installing the system while trying to maintain the existing system in other parts of the building. Additionally, our team had to closely engineer a system that attempted to follow the boundaries of the various construction phases, which required work in occupied and unoccupied areas. Pre-fabrication and quality control were a key component in dealing with these life safety systems. The new lighting control system was equally as complicated given the electrical circuiting for the corridor and egress emergency lighting did not necessarily follow the path of phased construction boundaries. Our team had to be creative of keeping existing lighting circuits energized while modifying and installing the new control system. As new remodeled areas were brought online, so were the new energy efficient lighting controls and emergency lights. Our team successfully deployed pre-fabricated components to speed the process and cut back on field labor.
Central Electric’s Project Manager reviewed the project plan drawings and specifications, including specialized building and construction requirements to ensure compliance with all aspects of the installation in sensitive work areas. This review included the identification of special equipment for handling and rigging switchgear, establishing procedures for receiving material deliveries and scheduling electrical outages. To meet the aggressive completion milestones, Central Electric developed its pre-fabrication and delivery schedule to reduce on-site installation time to the greatest extent possible. The plan required extensive coordination between trades and divisions of work to ensure sequencing and scheduling for installation and pre-fabrication of installed components. Central Electric’s approach for the project includes adherence to strict Safety Policies at the corporate/organizational level down to the specific project level job hazard analysis and measures to ensure safety for all aspects of work performed.
Through Central Electric’s dedication to incorporate project management best practices in its approach, it was able to complete the project with zero safety incidents, no added days for the project’s duration and on budget. Furthermore, the newly improved Davis Middle School facility will continue to serve students in San Antonio for decades to come.
Electrical Scope of Work
Central Electric was subcontracted by Joeris General Contractors to provide its electrical construction services including:
-
Mobilization
-
Branch Conduit and Boxes
-
Branch Wiring
-
Feeder Conduit
-
Feeder Wiring
-
Distribution/Gear Installation
-
Fixture Installation and Trim Out
-
Low Voltage Rough-In
-
Gear Distribution Package
-
Light Fixture Package
As mentioned above, Central Electric was required to perform the work during the summer months due to the school year cycle. These challenges were mitigated through effective communication with the project team to ensure that critical work was executed with zero errors or delays. Additionally, Central Electric was able to propose design plan reconfiguration of the electrical systems supporting the freezer and refrigeration equipment and expansion.
To overcome these challenges, the project team devised a plan that implemented “push-pull planning” and close coordination with all contractors to closely monitor and plan street closures, crane permitting for manholes and the re-design of the electrical switchgear for breaker placements to accommodate incoming feeds. Central Electric mitigated this challenge by pre-fabricating all of the utility yard conduits at their facility, transported the raceways and installed on-site once access was available. Additionally, lead-men were assigned to each of the major tasks (site work, electrical distribution, utility yard, finish-out, etc.) who all reported back to the on-site foreman for progress reporting.
An example of an innovative Project Management approach included the use of specialized equipment and software technology such as Plan Grid, Blue Beam and Site Docs. This technology was leveraged to assist with daily online reporting, which was distributed to the Project Team highlighting project issues and communication of critical information. Central Electric was also able to create a link for the client to evaluate progress and real-time completion of tasks as they occurred. The use of technology provided greater awareness of project issues between all parties. The use of Plan Grid assisted in keeping documents up to date in the field, including pre-fabricated elements, while ultimately reducing the turnaround time between current daily progress and updated plan drawings.
From a site safety perspective, Site Docs was used for weekly Toolbox Talks meetings and to collaborate with the Prime Contractor regarding awareness of safety requirements and specific job hazard analysis. Site Docs also assisted in streamlining daily reports and electronic submittals. Through incorporating project management best practices in its approach, Central Electric was able to complete the project with zero safety incidents, no added days for the project’s duration and on budget.