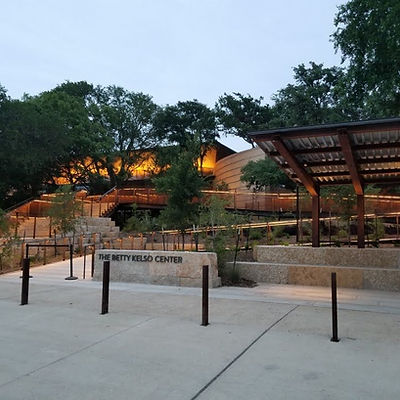
APPLEWHITE WAREHOUSE II
In 2003, Toyota Motor Corporation established Toyota Motor Manufacturing Texas, Inc. in San Antonio, Texas to produce the Tundra full-size pickup truck and the Tacoma mid-side pickup truck. In order to meet the manufacturing and logistical needs to produce both vehicles, Toyota selected a 2,000-acre site on the far south side of San Antonio for the new 2,000,000 square foot plant. During the plant’s construction, Toyota determined that additional vehicle production capacity would be possible by attracting on-site suppliers and support operations near the plant’s site. After Toyota invested $1.2 billion, the plant was able to begin manufacturing operations in November 2006. Following the plant’s development, it became apparent to local developers those additional facilities would be required to develop assets and infrastructure to compliment the manufacturing operations at the plant. Thus, additional corridors adjacent to the Toyota manufacturing plant were identified along Applewhite Road, which provides the primary access for the Toyota Manufacturing Plant and the Texas A&M University – San Antonio campus. As part of this development, Reyes Automotive Group II and Reyes Hayashi Automotive (RHA), which are both Tier I Suppliers for Toyota Motor Manufacturing Texas Inc., set their sights on the Applewhite Road. Along with his joint venture partner Hayashi Telempu North America, Reyes Automotive Group II leads the manufacturing of interior trim parts and carpeting for the Toyota Tundra and Tacoma Trucks.
Foreseeing the demand for suitable facilities along the industrial and commercial corridor, Reyes Properties contracted DBKO Design + Build to construct a new single-story warehouse building on Applewhite Road. As part of the DBKO Construction team, Central Electric was subcontracted to provide Electrical construction services including full electrical distribution system, electrical design build drawings, branch wiring and conduit box installation, underground sitework, and fabrication of lighting, sensors, and lighting controls. The Applewhite Warehouse II was constructed utilizing concrete tilt wall panels supported on drilled pier foundations with interior steel columns and a grade supported floor slab. The site also included sufficient pavement areas for truck access, loading/unloading areas, and staff parking.
During the project’s planning, Central Electric’s Project Manager reviewed the International Building Codes and the International Energy Conservation Code to ensure all electrical work, lighting fixtures, control systems were designed, fabricated, and installed to meet standards for compliance. During the construction phase, additional changes to the design were incorporated at the request of the client, which were to accommodate the specialized electrical and lighting needs of future tenants. Despite the changes directed by the client, Central Electric was able to negotiate with the lighting supplier to meet the additional requirements for the configuration change and fixture upgrades at no additional cost to the owner. Another critical cornerstone to Central Electric’s approach for the project includes adherence to strict Safety Policies at the corporate/organizational level down to the specific project level job hazard analysis and measures to ensure safety for all aspects of work performed.
Through Central Electric’s dedication to incorporate project management best practices in its approach, it was able to complete the project with zero safety incidents, no added days for the project’s duration and on budget. Furthermore, the new Applewhite Warehouse II facility will continue to add to the strong economic impact of Toyota’s investment and operations in San Antonio’s southwest side.
Electrical Scope of Work
Central Electric was subcontracted by DBKO Design + Build to provide electrical construction services including:
-
Project management
-
Design Build Electrical Drawings
-
Pre-fabrication, delivery, and installation of full electrical distribution system
-
Branch wiring and conduit box installation
-
Underground sitework
-
Fabrication of lighting, sensors, and lighting controls
-
Quality assurance and quality control
Due to agreed completion date, Central Electric sought to avoid any potential delays by performing two and three week “look ahead” planning which consisted of analyzing the project scope’s Work Breakdown Structure, extensive pre-construction planning to identify critical paths, workflows, resource allocations, risks, accounting of lead time for sourced components. Central Electric maintained an aggressive installation pace until project team experienced an abundance of wet weather at the project site which reduced the window for installation activities. The risk of schedule delays was mitigated by Central Electric’s conscious use of Project Management practices to provide the necessary awareness to achieve efficiencies on other aspects of the installation. Through Central Electric’s dedication to incorporating project management best practices in its approach, it was able to complete the project with zero safety incidents, no added days for the project’s duration and on budget.
Central Electric also utilized it’s on staff Engineering team to provide design build services for the Electrical distribution. This proved to be a vital component in streamlining the owners quickly changing requirements quickly, accurately, and immediately.
An example of Central Electric’s innovative Project Management approach included the use of specialized equipment and software technology such as Trimble Total Station, Plan Grid, Blue Beam and Site Docs. Central Electric leveraged technology to assist in laying out lighting and equipment locations and to ensure that the additional design changes requested by the owner were addressed on site. Technology was also utilized by the Central Electric for daily online reporting, which was distributed to the Project Team highlighting project issues and communication of critical information. Central Electric was also able to create a link for the client to evaluate progress and real-time completion of tasks as they occurred. Ultimately, the use of technology provided greater awareness of project issues between all parties. The use of Plan Grid assisted in keeping documents up to date in the field, including prefabricated elements, while ultimately reducing the turnaround time between current daily progress and updated plan drawings.
From a site safety perspective, Site Docs was used for weekly Toolbox Talks meetings and to collaborate with the General Contractor regarding awareness of safety requirements and specific job hazard analysis. Site Docs also assisted in streamlining daily reports and electronic submittals.